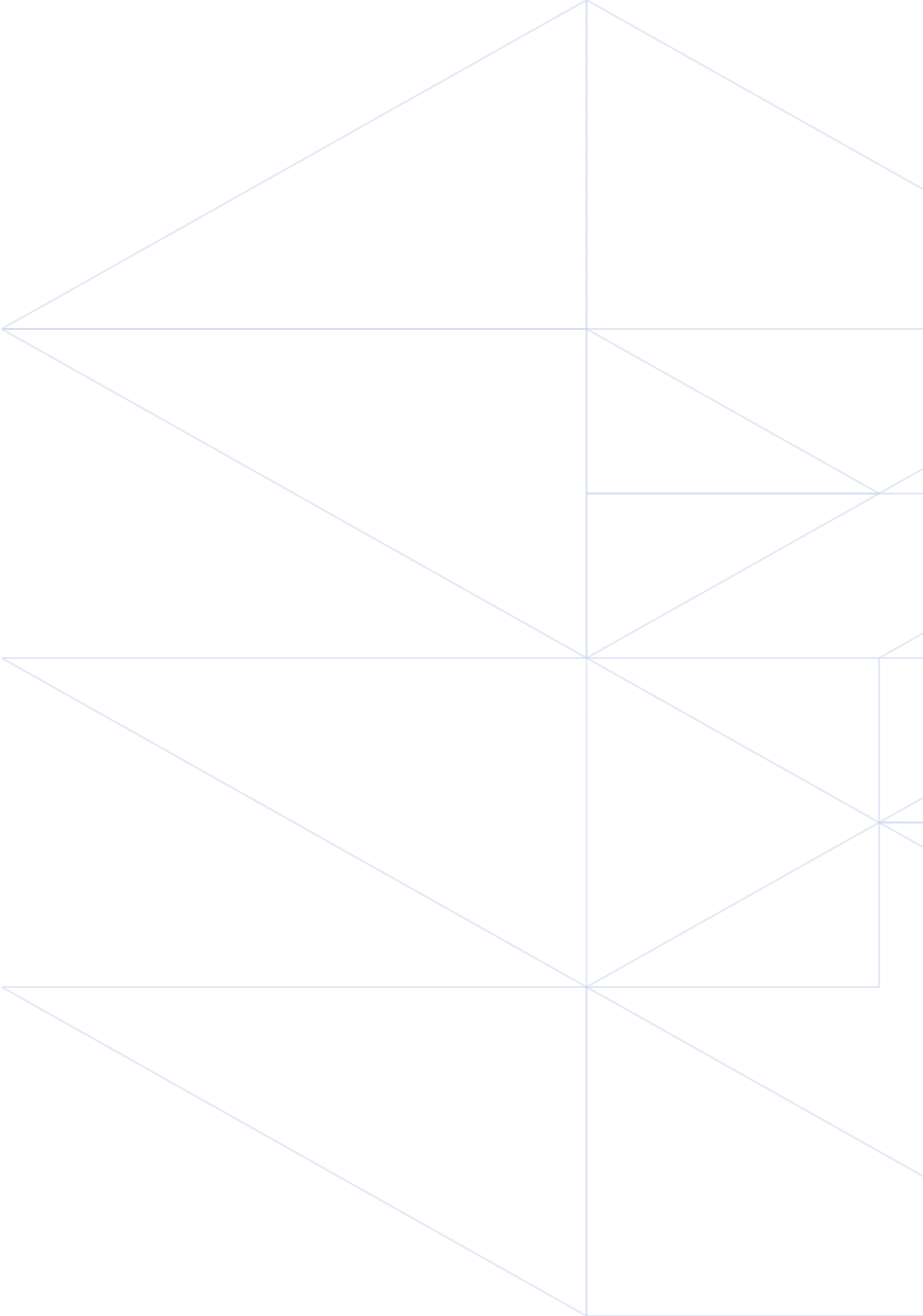
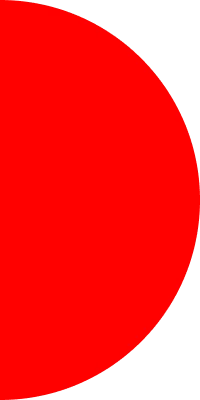
Frequently Asked Questions
Category
All
Yes, we have several standard absolute position options and can install most commercially available rotary sensors into the housing for our Rotary Position Sensors. These include the standard potentiometers, encoders with quadrature output and index pulse and resolvers. Please refer to the product data sheet or send a request to sales@tecnadyne.com with your specific requirements and we will see what we can do.
Tecnadyne hydraulic pumps are designed to operate from a wide variety of power sources, including regulated DC power supplies, filtered and rectified AC and batteries. There are a couple of important precautions that must be taken – the power source must have some capacitance to help filter the back EMF from the motors and precautions must be taken to isolate the instrument level signals from the main motor voltage and to prevent current loops. For a detailed explanation, please read Application Note AN605 – DC Brushless Motor Interface and Application Note AN601 – Back EMF and Ground Loops.
We recommend that you regulate the operating voltage of the hydraulic pumps so that it is within +/-15% of the rated voltage for that actuator. Remember, of course, that each model of pump is available at rated voltages from 48vdc to 330vdc (some models are available at rated voltages as low as 24vdc, and some are available to 500vdc). For more information on this subject, please read Application Note AN605 – DC Brushless Motor Interface.
Tecnadyne supplies its hydraulic pumps in three basic configurations. The first configuration simply mounts the pump to a DC brushless motor – the DC brushless motor is in a hard anodized aluminum housing and the pump is coated with a very rugged ceramic epoxy material. We refer to these as Hydraulic Pumps. The second configuration actually places the pump inside a hydraulic tank that includes a pressure compensator (to compensate for changes in hydraulic fluid volume due to leakage and depth changes). We refer to these as HPU’s and they have the advantage that the entire hydraulic supply (pump, tank & pressure compensator) is contained within one housing and that the pump is immersed in oil, which provides the best protection from the sea water. The third configuration, also referred to as HPU’s, integrates the pump, tank, and pressure compensator of the previous configuration with an internal manifold and four 4/3-way solenoid spool valves, pressure transducer, pressure and tank filters and hydraulic accumulator (if required). This third configuration of HPU provides an entirely self-contained hydraulic system – simply connect the A & B ports to the end effectors (cylinders, motors, etc.), connect power and RS485 signal and the system can be operated, but do consult the factory for special configurations to meet your specific system requirements.
Fixed displacement pumps are used when the hydraulic flow requirements are continuous and the flow rate is fixed – a constant speed winch, for example. Variable displacement pumps are used when the flow demand varies considerably (when used as a supply to a valve package controlling a manipulator or tool suite, for example) – when the flow requirements drop, the pump displacement drops to a level required to maintain system pressure and the electrical power demand drops accordingly. Since all Tecnadyne hydraulic pumps are powered by variable speed DC brushless motors, it is also possible to use a fixed displacement pump as a variable displacement pump – simply vary the motor speed as the hydraulic flow requirements increase and decrease. However, this does require that use the system hydraulic pressure to close the motor speed control loop. If you have any questions, please contact the factory.
Of course!
No, we are using the largest size rolling diaphragm that can be made on the available machinery.
The problem with the piston and seal type of pressure compensator is that one side of the piston is exposed to sea water and will eventually wear and leak. We use rolling diaphragms, which are made of neoprene reinforced nylon fabric and have the shape of a top hat. A spring- loaded piston fits within the hat and the outer ring of the hat is clamped between the two portions of the outer housing. The piston can move the full length of the outer housing and the top hat shaped diaphragm rolls between the piston and the housing wall. There is no friction, there is no sliding and there is nothing to wear out and leak.
Tecnadyne actuators are designed to operate from a wide variety of power sources, including regulated DC power supplies, filtered and rectified AC and batteries. There are a couple of important precautions that must be taken – the power source must have some capacitance to help filter the back EMF from the motors and precautions must be taken to isolate the instrument level signals from the main motor voltage and to prevent current loops. For a detailed explanation, please read Application Note AN605 – DC Brushless Motor Interface and Application Note AN601 – Back EMF and Ground Loops.
We recommend that you regulate the operating voltage to the linear actuators so that it is within +/-15% of the rated voltage for that actuator. Remember, of course, that each model of the Tecnadyne actuators is available at rated voltages from 48vdc to 330vdc (some models are available at rated voltages as low as 24vdc, and some are available to 500vdc). For more information on this subject, please read Application Note AN605 – DC Brushless Motor Interface.
Yes, in most cases our linear actuators can be back driven with a load that is 30-60% of the rated maximum. However, we do install electrical brakes on actuators when it is necessary that the actuator lock and not be back driven by the load.
Yes, there is a very small amount of backlash in the ball screw and nut. If backlash is critical, we can have the ball screw nuts hand fitted to the ball screws to reduce the backlash to almost immeasurable levels.
Yes, in most cases our linear actuators can be back driven with a load that is 30-60% of the rated maximum. However, we do install electrical brakes on actuators when it is necessary that the actuator lock and not be back driven by the load.
The linear actuators use O-rings or lip seals on the rods. The rods are polished using our proprietary process.
Yes, our linear actuators are oil filled and all include a pressure compensator (either integral with the actuator housing or as a separate unit) that compensates the internal pressure to the sea water ambient and compensates for the change of internal volume as the actuator rod extends and retracts.
The linear actuators are available with an encoder coupled to the motor shaft to give absolute position feedback. They are also available with internal or external limit switches and a digital pulse train output – using these it is possible to “home” the actuator to one limit or the other and then count pulses to determine position. Additionally, either the Model 194 Rotary Position Sensor or the Model 195 Linear Position Sensor can be installed in conjunction with the Linear Actuator.
Tecnadyne actuators are designed to operate from a wide variety of power sources, including regulated DC power supplies, filtered and rectified AC and batteries. There are a couple of important precautions that must be taken – the power source must have some capacitance to help filter the back EMF from the motors and precautions must be taken to isolate the instrument level signals from the main motor voltage and to prevent current loops. For a detailed explanation, please read Application Note AN605 – DC Brushless Motor Interface and Application Note AN601 – Back EMF and Ground Loops.
We recommend that you regulate the operating voltage to the rotary actuators so that it is within +/-15% of the rated voltage for that actuator. Remember, of course, that each model of the Tecnadyne actuators is available at rated voltages from 48vdc to 330vdc (some models are available at rated voltages as low as 24vdc, and some are available to 500vdc). For more information on this subject, please read Application Note AN605 – DC Brushless Motor Interface.
Yes, in most cases our rotary actuators can be back driven with a torque that is 30-60% of the rated maximum. However, we do install electrical brakes on actuators when it is necessary that the actuator lock and not be back driven by the load. Also, we have a special version of our Model 20 rotary actuator called the Model 20WD, that uses a worm drive gear assembly which cannot be back driven by the load on the shaft.
No.
We use a special compound O-ring which we have found to be very reliable when used on a highly polished shaft at low speeds (less than 150rpm). Tecnadyne has developed a proprietary process to polish the shafts and the final inspection of the shafts is under a 100-power microscope.
Yes, all of our rotary actuators are oil filled and pressure compensated using oil filled flexible tubing (Tygon) over the electrical conductors of the subsea cable.
We can supply the rotary actuators with a quadrature output signal generated by internal Hall devices with resolutions ranging from fifty pulses per revolution to over 10,000 pulses per revolution — the pulse count options available for each rotary actuator is determined by the output gear ratio of the actuator and other factors. Please consult the factory for available pulse counts for the rotary actuator model and speed desired. We can also supply rotary actuators with internal encoders, potentiometers, or resolvers.
No! It is necessary that your system has a time-based ramp from zero speed to full speed and from full speed to zero speed in both forward and reverse. If you are controlling the thrusters with a hand operated joystick, the time required to move the joystick from one position to another is probably enough for the thrusters. However, if you are driving the thrusters with a computer, it is essential that you program a linear ramp into the thruster control algorithm. The reason that this time-based ramp is necessary is because the thrusters generate back EMF, and the back EMF is much greater when the speed changes very rapidly. For example, if the time ramp from full power forward to full power reverse is 20ms, the back EMF current spikes will be 10-20 times greater than the steady state current (we have actually measured this). If this ramp is increased to 50ms, then the back EMF current spikes will be about 4-8 times the steady state current. And increase the ramp to over 100ms, and the current spikes will be about two times the steady state current. Make the ramp as long as you can and contact the factory if you have any questions.
Every Tecnadyne thruster goes through a rigorous test cycle. First, we test the electrical isolation of all subsea connector pins to the case of the thruster at 500v. Next, we pressure test the thruster in water to a pressure equivalent to the rated depth. And then, we repeat the electrical isolation test (this will indicate any water leaks). Once we know the thruster is not leaking, it is placed in our water test tank and is operated for a period of 30 minutes. We consider this test to be a break-in period. Finally, the thruster is operated throughout its normal operation cycle and all the performance data is collected and this is the final acceptance test of the thruster.
No! But if you do need to operate them out of water, do so for only a few seconds to verify that they are operating. If operated for too long, the sea water lubricated bearings will overheat.
All documentation is supplied via email. The supplied manual includes installation and integration instructions, field repair procedures, illustrated parts breakdown with parts list and schematics. We also include the final test reports for the thrusters.
Yes, please consult the factory.
The standard voltage rating for most thrusters is 48, 150, or 300vdc. Tecnadyne thrusters are available with voltages ranging from 24vdc to 500vdc (actual voltages available depends on the thruster model – please consult the data sheets).
Most Tecnadyne thrusters have a standard depth rating of 850m. All Tecnadyne thrusters are available with depth ratings to full ocean depth in a pressure balanced, oil filled configuration. However, sales of some thrusters with depth ratings greater than 1,000m require US Department of Commerce approval when these are shipped to some countries. Please consult the Tecnadyne factory for further information.
The thrusters have an MTBF of 20,000 hours. However, it is very important to remember that the propeller bearings are lubricated by the sea water. If the sea water is clean, the bearings will last for 2,000 hours. If the sea water is sandy (when operating on the bottom) the bearing life is severely reduced. It is easy to check for propeller bearing wear, just by rocking the propeller back and forth. And replacing the bearings takes only several minutes and the bearings are inexpensive.
Using a magnetic coupling eliminates the rotating propeller shaft and the shaft seal which are the major cause of leaks and failures with traditional thrusters. The propeller shaft seals in use today were all designed for use at or near the surface where the pressure is low – they inevitably fail when subjected to the pressure of typical ROV and AUV operations (100m to 10,000m). The magnetic couplings developed by Tecnadyne not only eliminate this common cause of failure, but the larger sizes are also able to reliably transmit over 20hp.
On most Tecnadyne thrusters, the propellers are held in place with a simple E-clip that can be removed with a screwdriver or an adjustable wrench. On the Model 260 & Model 300 thrusters, the propeller is held in place with a shoulder bolt that requires a 1/8in Allen key (provided with the thrusters) to remove. The largest thrusters require a propeller removal jig for field removal of the propeller, but it can still be completed in several minutes.
Our thrusters are very low maintenance – simply remove the propeller and flush with fresh water, and dry after use. It takes about 30 seconds to do this with each thruster.
Most likely, this will cause a problem with ground loops and noise – please refer to Application Note AN601 – Back EMF and Ground Loops. Tecnadyne supplies an isolation card specifically intended to address this problem. This card, the ISO-4, is a 4-channel isolation amplifier that isolates four analog control signals (from your D/A card, for example) and also provides isolated 12vdc instrumentation power to four thrusters – it is highly recommended. Tecnadyne also supplies the ISOMOD-4, ISOMOD-6 & ISOMOD-8, which are 4-channel, 6-channel, and 8-channel modules that package ISO-4 cards, with a capacitor bank, fuses and overvoltage protection in a 1-atmosphere housing depth rated to 2,000m standard, and deeper upon request. The ISOMOD-4, ISOMOD-6 & ISOMOD-8 can also be fitted with Tecnadyne’s ANALOG-8 card, which will control up to eight thrusters over an RS-232, RS-422 or RS-485 data link.
Tecnadyne thruster motors are designed to operate from a wide variety of power sources, including regulated DC power supplies, filtered and rectified AC and batteries. There are a couple of important precautions that must be taken – the power source must have some capacitance to help filter the back EMF from the motors and precautions must be taken to isolate the instrument level signals from the main thruster voltage and to prevent current loops. For a detailed explanation, please read Application Note AN605 – DC Brushless Motor Interface and Application Note AN601 – Back EMF and Ground Loops.
We recommend that you regulate the operating voltage to the thrusters so that it is within +/-15% of the rated voltage for that thruster. Remember, of course, that each model of the Tecnadyne thrusters is available at rated voltages from 48vdc to 330vdc (some models are available at rated voltages as low as 24vdc, and some are available to 500vdc). For more information on this subject, please read Application Note AN605 – DC Brushless Motor Interface
We recommend the tried-and-true approach — fabricate a saddle mount from aluminum, stainless steel, or plastic material that will partially encircle the cylindrical portion of the motor housing. Use two screw drive hose clamps (stainless steel) to hold the thruster to the saddle mount. Put electrical heat shrink tubing around the hose clamps — this will protect the thruster housing. And place a thin pad of stiff rubber between the thruster and the saddle mount. For more information this and other recommended mounting methods, please read the Application Note AN603 – Thruster Installation & Mounting. Tecnadyne can design and manufacture custom mounts upon request.
Recent projects include a 1000 ft-lb (1356 Nm) torque rated rotary actuator from 316 stainless steel, a 5600lb (25kN) force rated linear actuator with built in brake and encoder, a titanium full ocean depth rated valve pack and hydraulic power unit, and a thruster capable of operating to 1000 lbs. (454kg) thrust.
The answer is likely yes. Please contact our sales team at sales@tecnadyne.com
Tecnadyne offers custom design and manufacturing services for everything from complete systems to individual components. Our in-house engineering team has over 75 years of experience in the subsea industry. Our propellers, magnetic couplings, electronics, housings, and thruster gear trains are all designed by us, and most metal and plastic parts are manufactured in our CNC machine shop. From propellers optimized for efficiency at specific vehicle speeds to complete hydraulic systems, we can design and build anything your application requires.
Design Services
Recent projects include a 1000 ft-lb (1356 Nm) torque rated rotary actuator from 316 stainless steel, a 5600lb (25kN) force rated linear actuator with built in brake and encoder, a titanium full ocean depth rated valve pack and hydraulic power unit, and a thruster capable of operating to 1000 lbs. (454kg) thrust.
The answer is likely yes. Please contact our sales team at sales@tecnadyne.com
Tecnadyne offers custom design and manufacturing services for everything from complete systems to individual components. Our in-house engineering team has over 75 years of experience in the subsea industry. Our propellers, magnetic couplings, electronics, housings, and thruster gear trains are all designed by us, and most metal and plastic parts are manufactured in our CNC machine shop. From propellers optimized for efficiency at specific vehicle speeds to complete hydraulic systems, we can design and build anything your application requires.
Thrusters
No! It is necessary that your system has a time-based ramp from zero speed to full speed and from full speed to zero speed in both forward and reverse. If you are controlling the thrusters with a hand operated joystick, the time required to move the joystick from one position to another is probably enough for the thrusters. However, if you are driving the thrusters with a computer, it is essential that you program a linear ramp into the thruster control algorithm. The reason that this time-based ramp is necessary is because the thrusters generate back EMF, and the back EMF is much greater when the speed changes very rapidly. For example, if the time ramp from full power forward to full power reverse is 20ms, the back EMF current spikes will be 10-20 times greater than the steady state current (we have actually measured this). If this ramp is increased to 50ms, then the back EMF current spikes will be about 4-8 times the steady state current. And increase the ramp to over 100ms, and the current spikes will be about two times the steady state current. Make the ramp as long as you can and contact the factory if you have any questions.
Every Tecnadyne thruster goes through a rigorous test cycle. First, we test the electrical isolation of all subsea connector pins to the case of the thruster at 500v. Next, we pressure test the thruster in water to a pressure equivalent to the rated depth. And then, we repeat the electrical isolation test (this will indicate any water leaks). Once we know the thruster is not leaking, it is placed in our water test tank and is operated for a period of 30 minutes. We consider this test to be a break-in period. Finally, the thruster is operated throughout its normal operation cycle and all the performance data is collected and this is the final acceptance test of the thruster.
No! But if you do need to operate them out of water, do so for only a few seconds to verify that they are operating. If operated for too long, the sea water lubricated bearings will overheat.
All documentation is supplied via email. The supplied manual includes installation and integration instructions, field repair procedures, illustrated parts breakdown with parts list and schematics. We also include the final test reports for the thrusters.
Yes, please consult the factory.
The standard voltage rating for most thrusters is 48, 150, or 300vdc. Tecnadyne thrusters are available with voltages ranging from 24vdc to 500vdc (actual voltages available depends on the thruster model – please consult the data sheets).
Most Tecnadyne thrusters have a standard depth rating of 850m. All Tecnadyne thrusters are available with depth ratings to full ocean depth in a pressure balanced, oil filled configuration. However, sales of some thrusters with depth ratings greater than 1,000m require US Department of Commerce approval when these are shipped to some countries. Please consult the Tecnadyne factory for further information.
The thrusters have an MTBF of 20,000 hours. However, it is very important to remember that the propeller bearings are lubricated by the sea water. If the sea water is clean, the bearings will last for 2,000 hours. If the sea water is sandy (when operating on the bottom) the bearing life is severely reduced. It is easy to check for propeller bearing wear, just by rocking the propeller back and forth. And replacing the bearings takes only several minutes and the bearings are inexpensive.
Using a magnetic coupling eliminates the rotating propeller shaft and the shaft seal which are the major cause of leaks and failures with traditional thrusters. The propeller shaft seals in use today were all designed for use at or near the surface where the pressure is low – they inevitably fail when subjected to the pressure of typical ROV and AUV operations (100m to 10,000m). The magnetic couplings developed by Tecnadyne not only eliminate this common cause of failure, but the larger sizes are also able to reliably transmit over 20hp.
On most Tecnadyne thrusters, the propellers are held in place with a simple E-clip that can be removed with a screwdriver or an adjustable wrench. On the Model 260 & Model 300 thrusters, the propeller is held in place with a shoulder bolt that requires a 1/8in Allen key (provided with the thrusters) to remove. The largest thrusters require a propeller removal jig for field removal of the propeller, but it can still be completed in several minutes.
Our thrusters are very low maintenance – simply remove the propeller and flush with fresh water, and dry after use. It takes about 30 seconds to do this with each thruster.
Most likely, this will cause a problem with ground loops and noise – please refer to Application Note AN601 – Back EMF and Ground Loops. Tecnadyne supplies an isolation card specifically intended to address this problem. This card, the ISO-4, is a 4-channel isolation amplifier that isolates four analog control signals (from your D/A card, for example) and also provides isolated 12vdc instrumentation power to four thrusters – it is highly recommended. Tecnadyne also supplies the ISOMOD-4, ISOMOD-6 & ISOMOD-8, which are 4-channel, 6-channel, and 8-channel modules that package ISO-4 cards, with a capacitor bank, fuses and overvoltage protection in a 1-atmosphere housing depth rated to 2,000m standard, and deeper upon request. The ISOMOD-4, ISOMOD-6 & ISOMOD-8 can also be fitted with Tecnadyne’s ANALOG-8 card, which will control up to eight thrusters over an RS-232, RS-422 or RS-485 data link.
Tecnadyne thruster motors are designed to operate from a wide variety of power sources, including regulated DC power supplies, filtered and rectified AC and batteries. There are a couple of important precautions that must be taken – the power source must have some capacitance to help filter the back EMF from the motors and precautions must be taken to isolate the instrument level signals from the main thruster voltage and to prevent current loops. For a detailed explanation, please read Application Note AN605 – DC Brushless Motor Interface and Application Note AN601 – Back EMF and Ground Loops.
We recommend that you regulate the operating voltage to the thrusters so that it is within +/-15% of the rated voltage for that thruster. Remember, of course, that each model of the Tecnadyne thrusters is available at rated voltages from 48vdc to 330vdc (some models are available at rated voltages as low as 24vdc, and some are available to 500vdc). For more information on this subject, please read Application Note AN605 – DC Brushless Motor Interface
We recommend the tried-and-true approach — fabricate a saddle mount from aluminum, stainless steel, or plastic material that will partially encircle the cylindrical portion of the motor housing. Use two screw drive hose clamps (stainless steel) to hold the thruster to the saddle mount. Put electrical heat shrink tubing around the hose clamps — this will protect the thruster housing. And place a thin pad of stiff rubber between the thruster and the saddle mount. For more information this and other recommended mounting methods, please read the Application Note AN603 – Thruster Installation & Mounting. Tecnadyne can design and manufacture custom mounts upon request.
Pressure Compensators
Of course!
No, we are using the largest size rolling diaphragm that can be made on the available machinery.
The problem with the piston and seal type of pressure compensator is that one side of the piston is exposed to sea water and will eventually wear and leak. We use rolling diaphragms, which are made of neoprene reinforced nylon fabric and have the shape of a top hat. A spring- loaded piston fits within the hat and the outer ring of the hat is clamped between the two portions of the outer housing. The piston can move the full length of the outer housing and the top hat shaped diaphragm rolls between the piston and the housing wall. There is no friction, there is no sliding and there is nothing to wear out and leak.
Linear Actuators
Tecnadyne actuators are designed to operate from a wide variety of power sources, including regulated DC power supplies, filtered and rectified AC and batteries. There are a couple of important precautions that must be taken – the power source must have some capacitance to help filter the back EMF from the motors and precautions must be taken to isolate the instrument level signals from the main motor voltage and to prevent current loops. For a detailed explanation, please read Application Note AN605 – DC Brushless Motor Interface and Application Note AN601 – Back EMF and Ground Loops.
We recommend that you regulate the operating voltage to the linear actuators so that it is within +/-15% of the rated voltage for that actuator. Remember, of course, that each model of the Tecnadyne actuators is available at rated voltages from 48vdc to 330vdc (some models are available at rated voltages as low as 24vdc, and some are available to 500vdc). For more information on this subject, please read Application Note AN605 – DC Brushless Motor Interface.
Yes, in most cases our linear actuators can be back driven with a load that is 30-60% of the rated maximum. However, we do install electrical brakes on actuators when it is necessary that the actuator lock and not be back driven by the load.
Yes, there is a very small amount of backlash in the ball screw and nut. If backlash is critical, we can have the ball screw nuts hand fitted to the ball screws to reduce the backlash to almost immeasurable levels.
Yes, in most cases our linear actuators can be back driven with a load that is 30-60% of the rated maximum. However, we do install electrical brakes on actuators when it is necessary that the actuator lock and not be back driven by the load.
The linear actuators use O-rings or lip seals on the rods. The rods are polished using our proprietary process.
Yes, our linear actuators are oil filled and all include a pressure compensator (either integral with the actuator housing or as a separate unit) that compensates the internal pressure to the sea water ambient and compensates for the change of internal volume as the actuator rod extends and retracts.
The linear actuators are available with an encoder coupled to the motor shaft to give absolute position feedback. They are also available with internal or external limit switches and a digital pulse train output – using these it is possible to “home” the actuator to one limit or the other and then count pulses to determine position. Additionally, either the Model 194 Rotary Position Sensor or the Model 195 Linear Position Sensor can be installed in conjunction with the Linear Actuator.
Rotary Actuators
Tecnadyne actuators are designed to operate from a wide variety of power sources, including regulated DC power supplies, filtered and rectified AC and batteries. There are a couple of important precautions that must be taken – the power source must have some capacitance to help filter the back EMF from the motors and precautions must be taken to isolate the instrument level signals from the main motor voltage and to prevent current loops. For a detailed explanation, please read Application Note AN605 – DC Brushless Motor Interface and Application Note AN601 – Back EMF and Ground Loops.
We recommend that you regulate the operating voltage to the rotary actuators so that it is within +/-15% of the rated voltage for that actuator. Remember, of course, that each model of the Tecnadyne actuators is available at rated voltages from 48vdc to 330vdc (some models are available at rated voltages as low as 24vdc, and some are available to 500vdc). For more information on this subject, please read Application Note AN605 – DC Brushless Motor Interface.
Yes, in most cases our rotary actuators can be back driven with a torque that is 30-60% of the rated maximum. However, we do install electrical brakes on actuators when it is necessary that the actuator lock and not be back driven by the load. Also, we have a special version of our Model 20 rotary actuator called the Model 20WD, that uses a worm drive gear assembly which cannot be back driven by the load on the shaft.
No.
We use a special compound O-ring which we have found to be very reliable when used on a highly polished shaft at low speeds (less than 150rpm). Tecnadyne has developed a proprietary process to polish the shafts and the final inspection of the shafts is under a 100-power microscope.
Yes, all of our rotary actuators are oil filled and pressure compensated using oil filled flexible tubing (Tygon) over the electrical conductors of the subsea cable.
We can supply the rotary actuators with a quadrature output signal generated by internal Hall devices with resolutions ranging from fifty pulses per revolution to over 10,000 pulses per revolution — the pulse count options available for each rotary actuator is determined by the output gear ratio of the actuator and other factors. Please consult the factory for available pulse counts for the rotary actuator model and speed desired. We can also supply rotary actuators with internal encoders, potentiometers, or resolvers.
Hydraulic Pumps & HPU's
Tecnadyne hydraulic pumps are designed to operate from a wide variety of power sources, including regulated DC power supplies, filtered and rectified AC and batteries. There are a couple of important precautions that must be taken – the power source must have some capacitance to help filter the back EMF from the motors and precautions must be taken to isolate the instrument level signals from the main motor voltage and to prevent current loops. For a detailed explanation, please read Application Note AN605 – DC Brushless Motor Interface and Application Note AN601 – Back EMF and Ground Loops.
We recommend that you regulate the operating voltage of the hydraulic pumps so that it is within +/-15% of the rated voltage for that actuator. Remember, of course, that each model of pump is available at rated voltages from 48vdc to 330vdc (some models are available at rated voltages as low as 24vdc, and some are available to 500vdc). For more information on this subject, please read Application Note AN605 – DC Brushless Motor Interface.
Tecnadyne supplies its hydraulic pumps in three basic configurations. The first configuration simply mounts the pump to a DC brushless motor – the DC brushless motor is in a hard anodized aluminum housing and the pump is coated with a very rugged ceramic epoxy material. We refer to these as Hydraulic Pumps. The second configuration actually places the pump inside a hydraulic tank that includes a pressure compensator (to compensate for changes in hydraulic fluid volume due to leakage and depth changes). We refer to these as HPU’s and they have the advantage that the entire hydraulic supply (pump, tank & pressure compensator) is contained within one housing and that the pump is immersed in oil, which provides the best protection from the sea water. The third configuration, also referred to as HPU’s, integrates the pump, tank, and pressure compensator of the previous configuration with an internal manifold and four 4/3-way solenoid spool valves, pressure transducer, pressure and tank filters and hydraulic accumulator (if required). This third configuration of HPU provides an entirely self-contained hydraulic system – simply connect the A & B ports to the end effectors (cylinders, motors, etc.), connect power and RS485 signal and the system can be operated, but do consult the factory for special configurations to meet your specific system requirements.
Fixed displacement pumps are used when the hydraulic flow requirements are continuous and the flow rate is fixed – a constant speed winch, for example. Variable displacement pumps are used when the flow demand varies considerably (when used as a supply to a valve package controlling a manipulator or tool suite, for example) – when the flow requirements drop, the pump displacement drops to a level required to maintain system pressure and the electrical power demand drops accordingly. Since all Tecnadyne hydraulic pumps are powered by variable speed DC brushless motors, it is also possible to use a fixed displacement pump as a variable displacement pump – simply vary the motor speed as the hydraulic flow requirements increase and decrease. However, this does require that use the system hydraulic pressure to close the motor speed control loop. If you have any questions, please contact the factory.
Position Sensors
Yes, we have several standard absolute position options and can install most commercially available rotary sensors into the housing for our Rotary Position Sensors. These include the standard potentiometers, encoders with quadrature output and index pulse and resolvers. Please refer to the product data sheet or send a request to sales@tecnadyne.com with your specific requirements and we will see what we can do.
Sales & Customer Support
sales@tecnadyne.com